Common Components of an MDR Conveyor System
If you’ve spent time recently shopping around for MDR conveyor, you’ve probably heard the word modular thrown around. In fact, it seems the word modular has become almost synonymous with MDR conveyor around the industry. But what does that actually mean?
"Modular" MDR conveyor lines include a wide variety of system components that come in different shapes and sizes, that do different things in terms of how they convey material. In the end all these components fit together nicely (think puzzle pieces, or Legos) and result in a full system made up of smaller pieces that seamlessly connect.
The modular nature of these systems allows for providers to build complex, customized layouts to fit their clients' conveying needs using a variety of these system components to achieve an intelligent and efficient flow. These types of systems lend perfectly to industries requiring high throughput for medium or light loads of different types of material.
Each provider has their own unique quirks and capabilities for each of all system components, so be sure to spend time finding the right provider for you. That being said, there are many baseline MDR conveyor system components that all providers have and any potential buyer should be familiar with. These components are the building blocks of your future conveyor system. Knowing what’s out there is critical to ensuring you have all the options on the table for designing your system and achieving your throughput and other operational goals.
This article will provide an overview of the most common MDR conveyor system components, give a brief explanation of how they operate and explain what their application is in the conveyor system itself.
Straights

Straight MDR conveyor sections are the simplest component and the bread and butter of almost any conveyor system, making up the vast majority of what actually ends up in a warehouse. They are often used as the baseline for the system, determining things like between-frame width, top of roller height, roller distance, zone lengths and other specifications that the all the other system components will be based off of. When you are first getting started building out an MDR conveyor system, naturally you will start by identifying what product or products you are conveying, then work with suppliers to find the right type of conveyor for that product. Most often, you’ll be using straight sections through this determination process because of their simplicity.
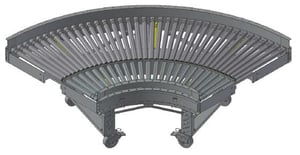
Curves
Curved MDR conveyor sections can refer to a variety of different components that allow for products to change direction using a curve. Most MDR conveyor suppliers offer a wide variety of curve types to fit whatever the system’s directional change requirements are. These include slight curves with as little directional change as 45-degrees, or 90-degree turns and all the way up to complete 180-degree turns.
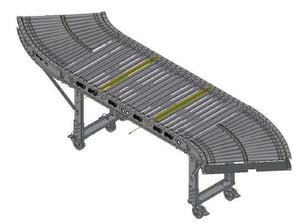
There is also a type of curve component commonly referred to as an “S-Curve” (pictured to the right) where product is traveling in one direction, enters a slight curve that then immediately recorrects and repositions the product so that it is traveling in the same initial direction but is shifted over. These are used when you need to redirect conveyor around something on the warehouse floor such as a support column or workstation but ensure the product continues traveling in the same direction.
Lift Gates
Lift gate sections provide easy and safe access to locations in a warehouse otherwise blocked by the conveyor system. They are powered and otherwise mostly appear like straights, but they include hinges that allow for either manual or automatic lifting of the straight section so workers can travel through the gate to other work areas.
Diverters
Diverter MDR sections automatically divide products from one or several input lanes into two or more output lanes. Diverters can consist of a wide variety of different mechanisms to split products into different output lanes, such as pushers, pop-ups, cross belts, tilt trays, push trays and more. All these different types of diverters fall into the sortation category of MHE equipment. If you'd like to learn more about the specifics of these, be sure to check out our three part series covering Automated Sortation Systems: Part One, Part Two and Part Three.
Mergers
Merge sections are the exact opposite of diverts. They automatically combine multiple input lanes into a single output lane. There are three primary types of mergers used in modern material handling: sawtooth, combiner and staging mergers. Sawtooth mergers operate on a “space available” logic and use accumulation technology to slip a parcel into an already moving output line when there is an opening for it. Combiner mergers take running parallel lines that feed into a single wide combining section with guards that gradually push products together and release them one at a time. Staging mergers are similar to Sawtooth mergers but can achieve much higher throughput rates by preparing long groups of product spaced out along staging conveyor, then merging these densely packed streams of product into the output belt at a faster rate than Sawtooth mergers, which input product a few at a time.
Skews
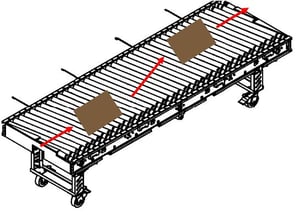
Skew sections direct packages towards one side of the conveyor frame using angled (skewed) rollers as they move along the conveyor bed. Skews are available in left-hand or right-hand modes that determine which side of the conveyor the product is pushed to. There is another type of Skew section commonly referred to as a “Herringbone” section where parallel sets of angled rollers move product to the centerline position on the conveyor bed. This function might be required when entry into another conveyor section is needed for proper downstream operations to be performed successfully.
Contact
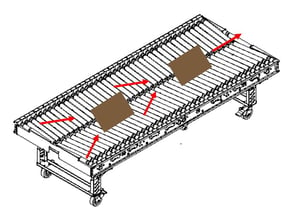
CCS Specializes in MDR Conveyor. We offer run-on-demand MDR Conveyor, MDR Spirals, Mobile MDR Conveyor and MDR Pallet Conveyor. If you’re interested in learning more about any of these types of conveyor, please contact Joel Thomas by email at joelthomas@cartercontrols.com or by phone at 240-815-1835.